What is it?
CutLayer builds large, near net shape additive parts, from any material that can be machined. Like our LSAM extruder based additive printers, parts are made in layers, stacked on top of one another, resulting in a hollow shell. However, instead of extruding those layers, they are instead cut from sheets of material and assembled, using exclusive advanced technology.
Overview
The core idea behind CutLayer is a way to get the benefits of additive manufacturing using material that can’t be printed.
3D printing is generally what people think of when we say “additive manufacturing” when actually, additive manufacturing is making parts by adding material, rather than subtracting it. CutLayer is a whole new approach to doing just that, for large parts.
CutLayer is simply machining or cutting out layers of material and adding them on top of one another. It works with any material that can be cut or machined.
In order to efficiently cut the layers from sheet material, each layer needs to be separated into segments which can then be tightly nested for machining. The layer-segments are then re-assembled into complete layers.
CutLayer is a simple idea that, until now, didn’t make sense.
Although it can make large industrial parts, tools and molds at an almost unbelievably low cost, creating nested CNC programs to machine hundreds upon hundreds of individual layer-segments that must all precisely mesh together to make a single part is a monumental programming task, virtually impossible using traditional programming. It just doesn’t make sense. Programming cost would overwhelm any possible savings.
Now, with Thermwood’s CutLayer , the programming task is gone, leaving only the benefits.
This is only possible because of cutting edge Machine Intelligence. Instead of sending it a CNC program, Thermwood’s Cut Layer Additive machine has been taught, and so inherently knows, how to make CutLayer parts.
The only thing required to make a part using CutLayer is to tell the machine what you want to make.
This is done in two steps.
Step one is to “Send it the Shape” by sending it a CAD file, which defines the outer surface of the part. You don’t need a detail file, just the basic shape.
Step two is to “Tell it how you want it made”, that is, what material do you want to make it from, how thick do you want the walls, how much trim stock do you want, how many segments do you want on each layer, things like that. This is done interactively using dynamic graphics.
It’s simple enough that it can be done using a touch screen, right at the machine, or you can use a desktop, do it in the office and send it to the machine for processing. It takes a tiny fraction of the time it would otherwise take using traditional programming.
Once the machine knows what you want to make, it automatically creates the additive part and the layer segments needed to make it, nests them on your material and creates an internal multi tool program to cut it all out.
Dowel holes are machined between layers to assure assembly alignment, making assembly quick, easy and accurate.
It prints the layer number and position on each layer-segment to make sorting and final assembly really easy. It also prints a QR code in case you ever need to re-make that particular part.
When actually cutting, it guides the operator through the entire cut process, step by step. When nesting, it prioritizes parts from early layers so that you can begin assembly while the machine is still cutting.
Although assembly may sound involved, printed labels, precision machined joints and dowel alignment, make assembly surprisingly quick and easy. Overall, the entire process, cutting and assembly, takes, at most, the same amount of time as a thermoplastic additive printer takes to produce the same near net shape part.
With some material it’s even faster, sometimes a lot faster.
The final result is the ability to quickly make large, incredibly low-cost parts using an approach that, until now, didn’t make sense.
Advantages of CutLayer
- Parts produced using CutLayer are surprisingly low cost
- CutLayer production equipment is lower cost
- Large parts can be made from any material that can be machined, including non -ferrous metal
- It’s fast compared to other non-additive methods of making large industrial parts
- Unique products, such as highly filled thermoset composites, are possible
- There are few restrictions as to part geometry
- CutLayer Tooling with internal cooling lines are supported
- There is no practical limit to the size of part that can be produced
Thermwood’s CutLayer Machine (CLA Machine)
- Designed specifically for CutLayer manufacturing
- The machine KNOWS how to make a CutLayer part from a simple CAD model
- Automatically creates the nested CNC program needed to machine each layer in segments
- Adjusts layer-segment geometry to provide a specified trim stock
- Prints information on each segment telling you what layer it’s on
- Prints identifier on each segment telling you its position on that layer and what it connects to
- Prints a QR code on each part making it easy to re-machine a part, if ever needed
- Machines joints between layer-segments to connect them, to make full layers
- Drills dowel alignment holes to provide precise layer to layer alignment
- Prints dowel insertion markers on each part to further simplify assembly
- Staggers segment joints for a more solid structure
- Drills and taps attachment holes between two or more layers so that metal layers can be bolted together
- Machines internal passages for internal heating or cooling fluid (coming)
- Internal “Anchor Points” facilitate adding internal stiffening structure (coming)
- Tab construction keeps parts from moving during machining
- Automatic tool changer with up to 12 tools
- 13 HP, 24,000 RPM router head for fast machining
- 5’x12’ vacuum cutting table
Aerospace Layup Tool
Aerospace layup tool is made form epoxy-fused fiberboard with plural component urethane coating. it was made using about $2,000 worth of material in less time than it took to additively print the same part.
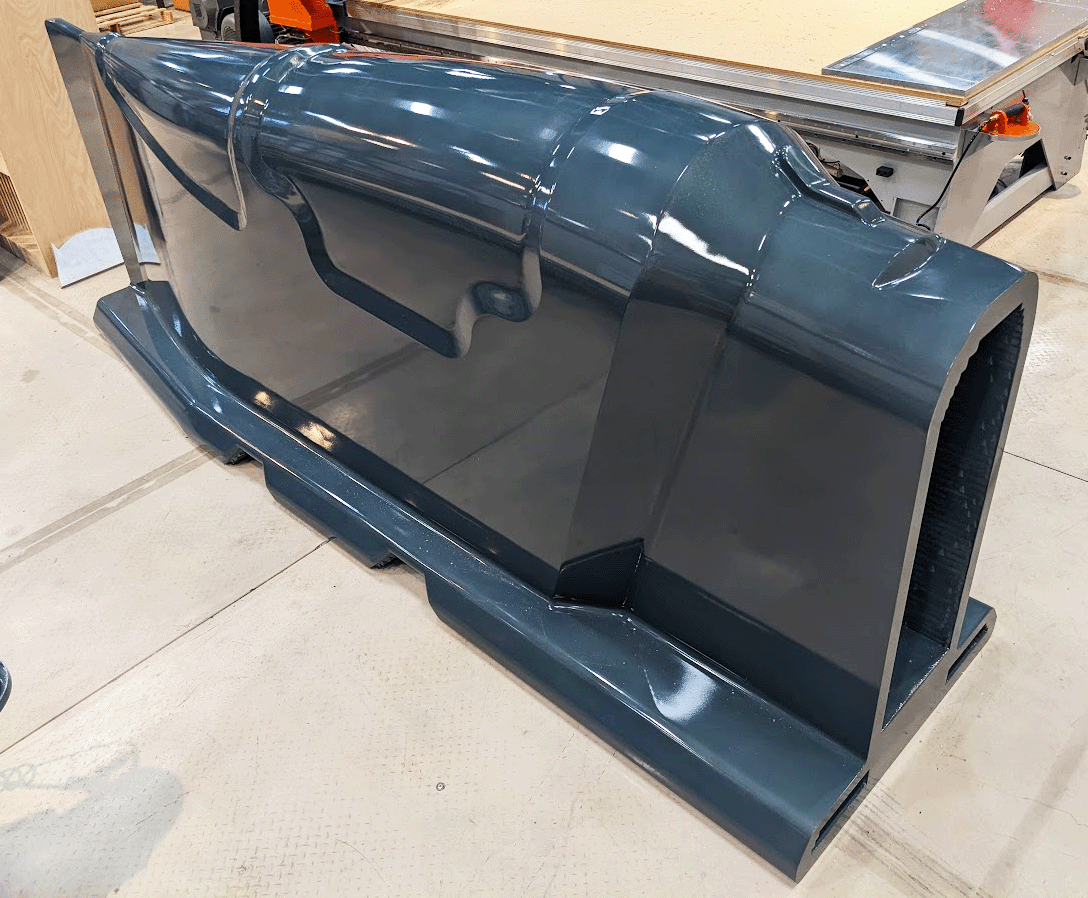
Aluminum Trim Fixture
Aluminum aerospace trim fixture made using cut layer additive process. Although it looks solid, the surfaces are all only about an inch thick, which means it uses a minimum amount of material.

Aluminum Thermoforming Mold
This is a CutLayer Thermoforming mold made of aluminum. It includes 3 vacuum chambers and 6 liquid channels, end to end, used to control mold temperature, all machined completely inside the 2” thick mold face.
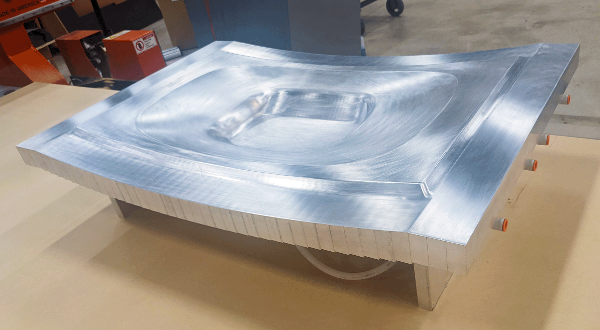
Drone Pattern
One of the first parts made using cut layer additive and less than $400 worth of material.
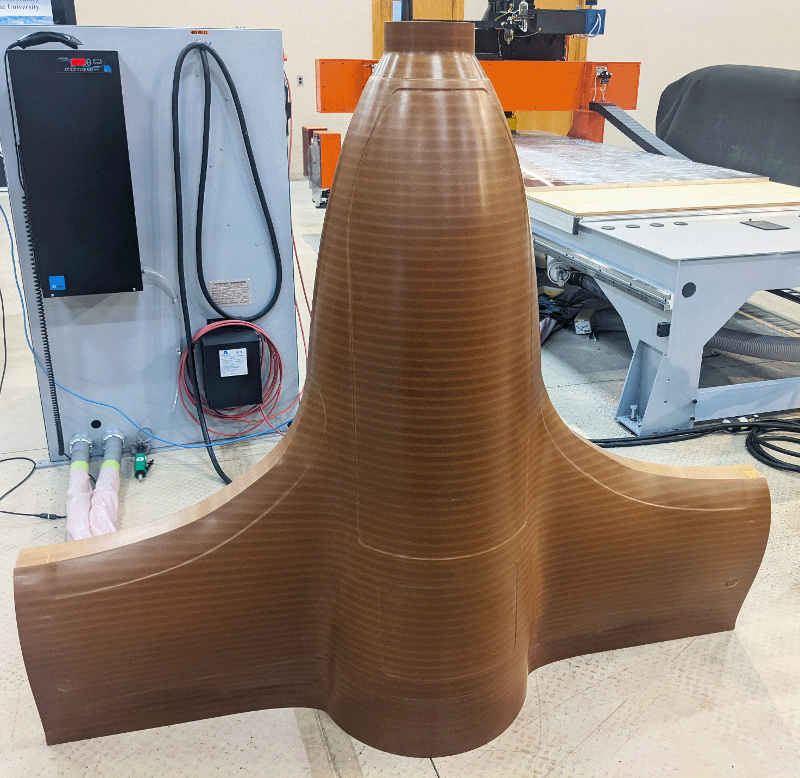
CutLayer Machine
Cut Layer Additive Machine with Advanced machine Intelligence, built specifically for the Cut Layer Additive process, costs considerably less than other large format near net shape additive systems.
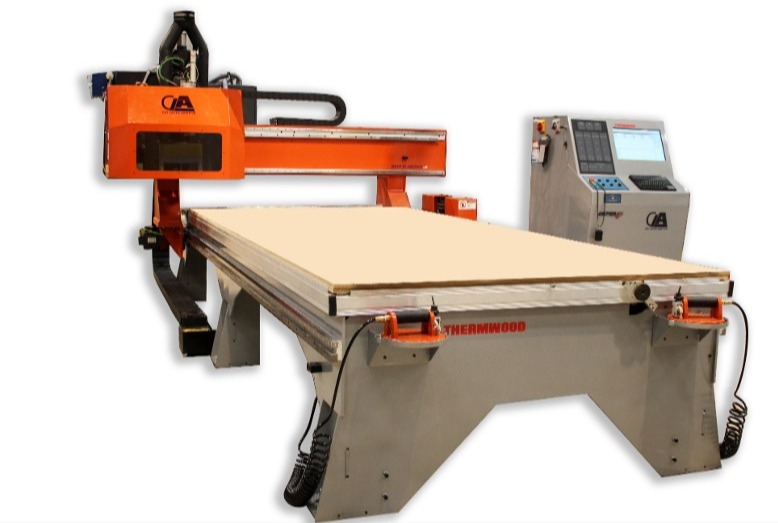
Machine Intelligence
Machine intelligence means you show the machine what you want using a simple interactive process that requires a tiny fraction of the time it would normally take using traditional programming.
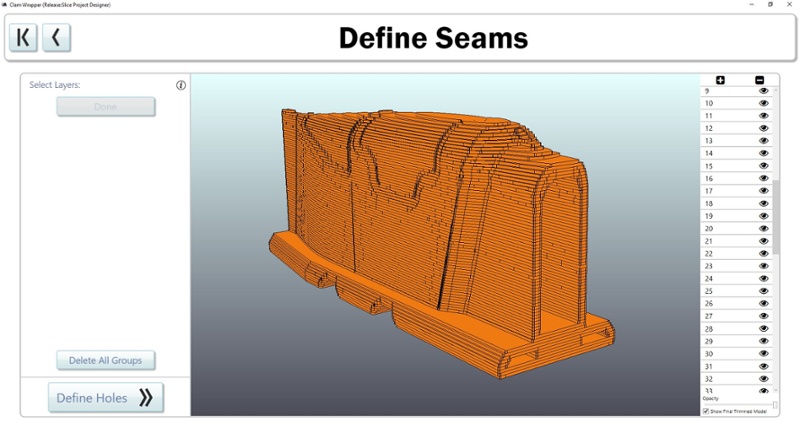
Efficient Nesting
Breaking layers into segments means highly efficient nesting. Unique joinery makes putting layers back together really easy.
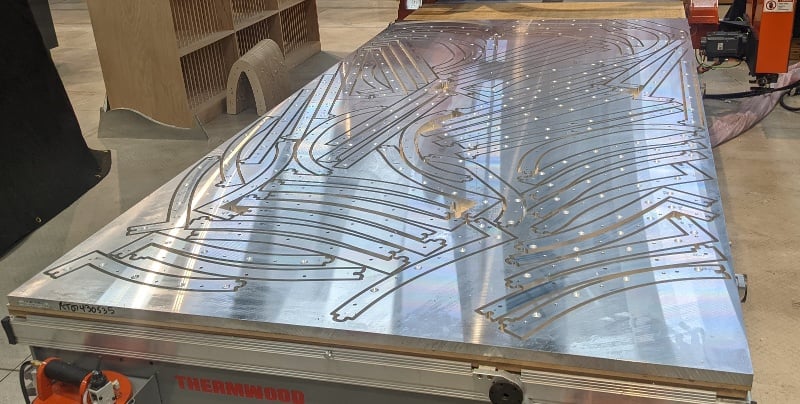
Easy Assembly
Machine printing tells you which layer the part is on, its position on the layer and where dowels need to be inserted, making assembly easy. QR code makes re-cutting the part easy, if you ever need to.
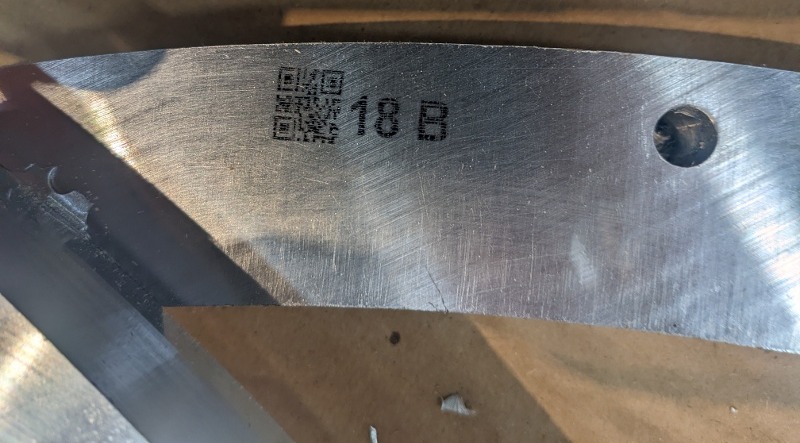
