The Secret to LSAM Print Quality… A Different Process
Prior to LSAM, 3D polymer printing was all done using essentially the same approach. Parts were printed with a small print bead onto a hot table, in a heated chamber, keeping the printed part hot until printing was complete.
While this worked reasonably well for smaller net shape parts, scaling the process up for large near-net-shape parts didn’t work quite as well.
A Different Approach
Thermwood took a fundamentally different approach with our LSAM large scale additive manufacturing system. Instead of printing with a small bead in a heated environment, Thermwood uses a large bead, printed at room temperature in an essentially “continuous cooling” process.
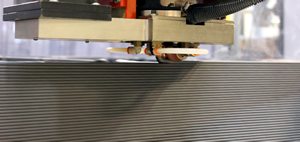
The beads are large enough, with enough heat energy, to completely fuse with the previous layer. Thermwood also employs a temperature controlled “compression wheel” to form the round melt coming from the print nozzle into a flattened bead and fuse it with the previous layer.
With this process, print speed is essentially controlled by the cooling rate of the polymer being printed, rather than by the output of the print head. The printed bead must cool enough to support the next layer, but must still be warm enough to fuse completely with it.
This means that there is a specific temperature range, which is different for each polymer, where this approach to printing works. Each polymer requires a certain amount of time to cool to within that temperature range. That amount of time is the fastest that a layer can be printed, regardless of its size.
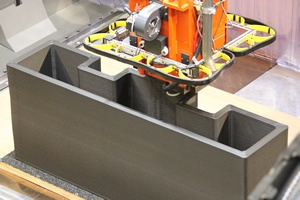
The output capacity of the print head simply determines how large a layer you can print in the amount of time available for each layer. Thermwood’s standard 40mm melt core can print layer lap lengths of over 200 ft. with most polymers. For even larger parts, Thermwood is working on an even larger melt core which can be retrofitted into the same print head housing as the 40mm core.
This process yields almost perfectly fused structures. Molds printed using the LSAM process routinely hold vacuum at elevated temperature and pressure in an autoclave without the need for any type of external coating.
Unique Part Hold Down Method
The only issue remaining was how to hold the parts during printing. In the previous process, polymer parts tend to stick to a heated table. Since Thermwood’s process doesn’t have a heated table, this wouldn't work. Also, since parts are both printed and trimmed on the same machine with LSAM, the part needed to be held for trimming after it was printed and cooled. Parts generally release from a heated table when they cool down.
LSAM's Patented "Bead Board"
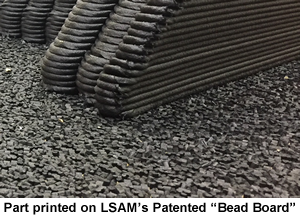
Thermwood’s approach to this requirement turned out to be quite unique. We developed a “bead board” to hold the parts both during printing and trimming.
The beard board consists of a plywood panel to which ABS pellets or “beads” are glued.
When a part is printed with this method, it fuses with the ABS beads holding it to the board, but one additional thing happens. Heat from the printed bead not only heats the ABS beads but also heats the glue holding them.
The glue softens enough that the beads can move on the board as the part cools and shrinks, eliminating cooling stresses that might otherwise be generated by a more rigid system. Once cool, the glue re-hardens holding the part securely for trimming. A couple of large screwdrivers and a hammer will remove the part once it is complete.
LSAM Printing - Final Thoughts
This print approach required an almost complete rethinking of the print head design, control system operation and software, and we will explore those issues later.
For now, know that LSAM printing, at its very core, is fundamentally different.
More Information on LSAM
LSAM is based on exciting new technology developed from an entirely new direction.
LSAM is intended for industrial production. It is not a lab, evaluation or demonstration machine, but is instead a full-fledged industrial additive manufacturing system intended for the production of large scale components.
Thermwood has already applied for over 45 separate patents on various aspects of this new technology (more than half of which have already been granted) and more will be coming as development continues. LSAM is truly “state of the art” in this exciting new world of Large Scale Additive Manufacturing.
