Ever wondered how you can produce large format, near-net-shape parts faster and more affordably? Check out this innovative use of Thermwood’s Cut Layer Additive process in action!
Watch as CLA creates a Trim and Drill Vacuum Fixture using RAKU Tool SB-0497 with remarkable precision and speed. This method slashes production costs while maintaining top-quality results. See how cutting layers, rather than printing them, is making large-scale manufacturing easier and more efficient than ever
Project Details:
- Trim and Drill Vacuum Fixture made from RAKU Tool SB-0497
- CLA Software Processing Time: 13 minutes 48 seconds
- CLA Machining Near Net Shape Layers Time: 1 hour 4 minutes
- Assembly Time: 2 hours with 2 employees
- Total 5 axis Trimming Time: 35 hours
Cut Layer Additive is a powerful new additive approach that produces large format, near-net-shape parts at incredibly low cost, using a lower cost additive machine. Unlike large format additive printers (like Thermwood’s LSAM), the new process makes large parts from a variety of materials that can’t be printed.
Cut Layer Additive parts are similar to large additively printed parts, in that they are essentially hollow structures made in layers. However, instead of printing the layers, they are instead cut from thick sheets.

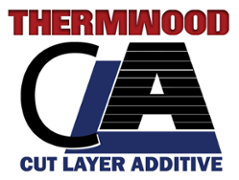