🎓 Congratulations to the 2025 Thermwood Scholarship Recipients! 🎓
Thermwood Corporation is proud to award $2,000 Renewal Scholarships to 12 outstanding seniors from the Class of 2025. These students have demonstrated exceptional dedication to academics, athletics, leadership, and their communities. We are proud to support their next chapter!
Anna Deorto – Daughter of Christina Balbach and David Deorto, and a graduate of Heritage Hills High School.
Anna was active in Cross Country, Swim, and Track, as well as Pep Club, Young Women Lead, and True Life Baptist Church, and served as a coach for Girls on the Run.
She will attend Vincennes University on an Athletic Scholarship to pursue a degree in Education.
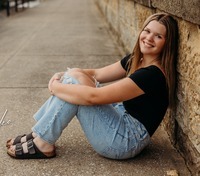
Bria Hayko – Daughter of Bill and Lisa Dotson of Tell City, IN, and a graduate with Academic Honors from Tell City High School. Bria was involved in Spanish Club, Pep Club, and played basketball and softball.
She will major in Exercise Science at Western Kentucky University.
Claudia Burton – Daughter of John and Angela Burton of Huntingburg, IN, and a Top 10% graduate of Southridge High School.
Claudia was active in BPA, FCA, Student Council, Key/Kindness Club, Spanish Club, and played Volleyball and Softball.
She plans to study Respiratory Therapy at the University of Southern Indiana.
Cruz Meece – Son of Natalie and Jeff Meece of Huntingburg, IN, and a graduate of Southridge High School.
Cruz was involved in FCA and the National Society, and participated in Football and Unified Track.
He plans to major in Exercise Science at Indiana University.
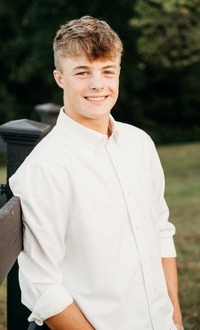
Elijah Meece – Also the son of Natalie and Jeff Meece, and a Top 10% graduate of Southridge High School.
Elijah participated in FCA, the National Society, and played Football and Track.
He will attend Purdue University to major in Construction Management.
Emma Hoffman – Daughter of Jeremy and LeeAnn Hoffman of Mariah Hill, IN, and an Academic Honors graduate of Heritage Hills High School.
Emma was a member of Fellowship of Christian Athletes and participated in Volleyball and Track.
She plans to major in Business Administration at Vincennes University Jasper Campus.
Jayden Klem – Daughter of Kyle Klem and Tonya Goerfrich, and a graduate of Heritage Hills High School.
Jayden was active in Young Women Lead, Pep Club, and Chess Club.
She plans to study Social Work at the University of Southern Indiana.
Logan Callahan – Son of Ryan and Mary Callahan and Kathryn and Matthew Brenner, and a graduate of Heritage Hills High School.
Logan was involved in the Santa Claus Christian Church Youth Group.
He will pursue a degree in Computer Science at the University of Southern Indiana.
Nigel Tretter – Son of Daniel and Jennifer Vonderheide and Michael and Kelly Tretter, and a Perfect Attendance graduate of Northeast Dubois High School.
Nigel was active in Beta Club, Student Council, Class Officer, FCA, and Spirit Club, and participated in Swim and Soccer.
He will major in Motorsports Engineering at Purdue University.
Olivia Vote – Daughter of Amanda and Nicolas Vote of Newburgh, IN, and a Collegebound AP Scholar graduate of Castle High School.
Olivia was active in Student Council, Theater, and French Club.
She will major in Chemistry at Purdue University.
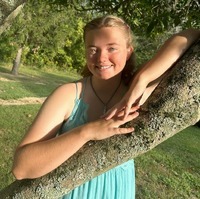
Shera Deno – Daughter of Jason and Rene Deno of Huntingburg, IN, and a graduate of Southridge High School.
Shera participated in Choir and was part of the school Musical.
She plans to attend Ivy Tech Community College to pursue Early Childhood Education.
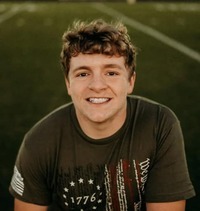
Waylon Willhite – Son of Jason and Rachel “Jones” Willhite of Rome, IN, and a graduate of Perry Central High School.
Waylon was involved in Track and Football.
In addition to his scholarship, Waylon has entered Thermwood’s Career Advancement Partnership, receiving additional assistance for his studies at Vincennes University Jasper in Advanced Manufacturing & Automation Technology, with a pathway to a future career at Thermwood Corporation.
Congratulations Graduates!
Please join us in congratulating these incredible students and wishing them continued success as they embark on their academic and professional journeys!