Explore the Game-Changing Melt Core System in Thermwood’s LSAM Technology
Thermwood has been pioneering Large Format Additive Manufacturing (LFAM) since 2016, leading the industry with our advanced LSAM systems. These machines offer more than just large-scale capabilities—they deliver an unmatched printing experience with superior print consistency, precise temperature control, and powerful slicing software.
In this series, we’ll take you through the exclusive benefits of LSAM technology, starting with our patented Melt Core System. Discover how this cutting-edge innovation redefines material processing to achieve faster, more reliable, and efficient large-scale 3D printing. Ready to explore the future of manufacturing? Dive in and see why Thermwood is the leader in LFAM!
- High output deposition rates
- Large consistent bead sizes
- Standard Melt Core producing over 200 lbs/hr (90.72 kg/hr)
- Optional Larger Melt Core producing over 500 lbs/hr (226.8 kg/hr)
- PID heater control to tightly maintain processing temperatures
- Up to 450° C (850° F) processing temperatures
- Custom Industrial Extruder Screw
- Compression Following Wheel (temperature-controlled)
Thermwood Patented Polymer Melt Pump
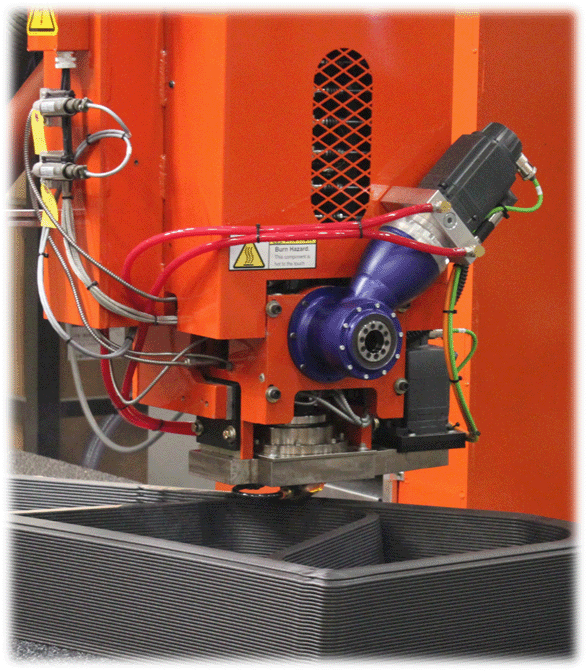
- Custom patented extruder screw design
- Provides a more consistent melt temperature
- Material flows from the extruder into a fixed displacement polymer melt pump system (patented)
- Melt Pump precisely delivers material to the nozzle
- Eliminates the problem of Extruder Surging
- Not necessary to change the extruder screw when switching between different materials
𝗦𝗲𝗲 𝘂𝘀 𝗹𝗶𝘃𝗲 at JEC 2025!
We will next be printing with material from a variety of suppliers on an LSAM AP 510 LIVE at JEC World 2025 in Paris, France (Hall 6 - Live Demo Area) on March 4th-6th. Visit our booth to learn more about LSAM, and you can always contact us directly to arrange a personal demonstration at our corporate headquarters.
Don't settle for less when it comes to your production process. Upgrade to Thermwood's LSAM system and take your manufacturing to the next level!
Learn more about LSAM.