
Thermwood and Purdue’s Composite Manufacturing & Simulation Center have been working together to develop and test methods of using 3D printed composite molds for the compression molding of thermoset parts. They have just announced that they have successfully been able to compression mold test parts using 3D printed composite tooling.
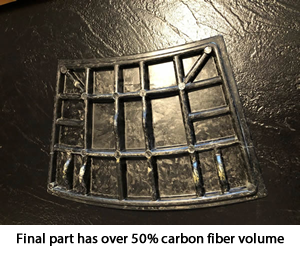
The test part, a half scale thrust reverser blocker door for a jet engine, was designed at Purdue and is approximately 10x13x2 inch in size. The two-part matched compression mold for the part was 3D printed using Techmer PM 25% carbon fiber reinforced PESU at Thermwood, using its LSAM large scale additive manufacturing system.
The mold halves were then machined to final size and shape on the same system. The completed tool was next taken to Purdue’s Composite Manufacturing & Simulation Center, in West Lafayette Indiana, where it was mounted to their 250 ton compression press. Parts were then molded from Dow’s new Vorafuse prepreg platelet material system with over 50% carbon fiber volume fraction.
The Details
Both halves of the mold were printed at the same time during a single 2 hour and 34 minute print cycle. When using Thermwood’s “continuous cooling” print process, the polymer cooling determines the cycle time for each layer, allowing both halves to be printed in the same time it would take to print one half (since both parts could be printed in the layer cooling time available).
Both halves of the mold were printed in less than 3 hours
Machining, however, must be done in the traditional manner, one part at a time, although there is an advantage to machining printed parts. Since the part is printed to near net shape, the overall amount of material that must be removed is significantly less than if the tool was machined from a solid block. Machining of the two mold halves required an additional 27 hours.
The first attempt at compression molding was not successful, but techniques were developed to account for the mechanical and thermal conductivity characteristics of the polymer print material and a second attempt produced acceptable parts.
The team determined that using printed composite molds in a compression press does require a significantly different approach than a tool for the same part machined from a block of metal. First, the tool must be internally heated since the polymer composite doesn’t transmit heat as well as metal. Thermwood developed a technique for deep hole boring of the printed composite part using the trim head on its LSAM machine, allowing the deep insertion of cartridge heaters.
A special heat control allows the temperature of various areas of the tool to be controlled independently, helping address the challenge of balancing the thermal characteristics of the thermoplastic composite mold with the processing temperature requirements of the thermoset material being processed.
Printed polymer composite mold must be heated and reinforced
Printed polymer composite mold must be heated and reinforced
Also, the outside of the mold must be reinforced so that the composite polymer used for the mold itself is under only compression loads and not tension during the molding operation, since forces developed during molding are greater than the tensile strength of the composite polymers used for the mold. This approach has successfully withstood molding pressure of 1,500 PSI during initial testing and the team believes even higher pressures are possible.
Parts were made on Purdue’s 250 ton compression press
Parts were made on Purdue’s 250 ton compression press
Parts were made on Purdue’s 250 ton compression press
Final Thoughts
Both Thermwood and Purdue believe this is an important first step in bringing additive manufacturing to compression molding. The speed and relatively low cost of printed compression tools has the potential to significantly modify current industry practices. Printed tools are ideal for prototyping and can potentially avoid problems with long lead time, expensive production tools by validating the design before a final version is built.
Additional development effort will be needed to further refine tool design and broaden the range of parts that this process will support, but all parties involved believe that this project demonstrates the viability of the basic approach.
Potential applications in the auto industry include prototyping and production tool verification. Because of high volume requirements for auto production, it is unlikely that these tools would function adequately for full production use, but actual useful production life is still unknown. It will require additional testing to determine just how many parts can be molded from an additive manufactured compression mold and what the ultimate failure mode actually is.
In aerospace, parts tend to be much larger and production volumes much lower, so it is possible that printed compression molds could find actual production use for larger, lower volume aerospace components, perhaps replacing open face tools and autoclaves for certain parts.
The relatively low cost and fast build rate of these additive molds significantly alters the decision matrix and timeline for developing new products using compression molding.
Purdue’s Composites Manufacturing & Simulation Center
The Composites Manufacturing & Simulation Center (CMSC) is a bridge between the academic and industrial communities, connecting the global composites industry and Indiana manufacturing to Purdue University. The CMSC research is driven by industry needs and grounded in academic rigor. Global sponsors and partners include aerospace and automotive OEMs, Tier 1 and 2 suppliers, materials suppliers, wind turbine manufacturers, and commercial software providers. The CMSC is a collaboration of the College of Engineering and the Purdue Polytechnic Institute and is a Purdue University Center of Excellence.
State-of-the-art manufacturing and characterization facilities provide a one-stop-shop for composites design, manufacturing, prototyping and model validation. Finally, the CMSC is dedicated to training engineers across the entire composites community in composites manufacturing and simulation.
Thermwood Corporation
Thermwood is a US based, multinational, diversified CNC machinery manufacturer that markets its products and services through offices in 11 countries. Thermwood is the oldest manufacturer of highly flexible 3 & 5 axis high-speed machining centers known as CNC routers.
Thermwood has also become the technology and market leader in large scale additive manufacturing systems for thermoplastic composite molds, tooling, patterns and parts with its line of LSAM (Large Scale Additive Manufacturing) machines that both 3D print and trim on the same machine. These are some of the largest and most capable additive manufacturing systems ever produced and are marketed to major companies in the aerospace, marine, automotive and foundry industries as well as military, government and defense contractors.
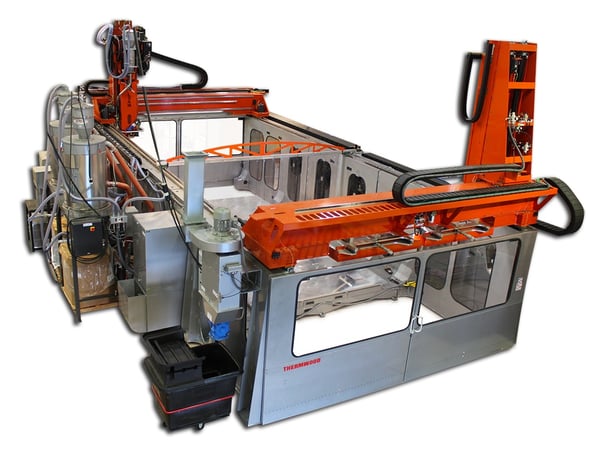
10’ x 20’ LSAM (Large Scale Additive Manufacturing)
