Written by Scott Burton - Sales Manager at Royce//Ayr
The latest kitchen design trends are demanding that solid wood and MDF doors appear in the same space with multi-colored cabinet layouts. This reality has challenged door makers to produce MDF doors that resemble solid wood profiles. Production limitations have traditionally made it impossible to make MDF doors on a CNC router that match solid wood doors made on traditional moulders and tennoners.
Advancements in MDF door tooling design and related software packages have made it possible to machine MDF doors on a CNC router that could pass as solid wood. A cohesive combination of smart tool design, flexible software, and proper material can produce an MDF product that is almost an exact match to solid wood once the door has been finished and installed.
The application is possible, but does require some critical tools and design strategy to achieve a door with tight corners and good surface finish that can be primed with minimal sanding. There are a couple of problems that must be overcome before achieving success.


Shows the current possibilities of MDF profiled doors on a CNC router. Notice the detailed moldings and small radius on the corners of the inside profile that can be achieved.
Problem # 1 - Moulding details and tight inside corners
In previous years, a simple profile made from a single pass with a profile tool would create a rounded corner affect that made it obvious to the customer that the door was made from MDF and machined from above with a CNC router bit. Detailed moldings and tight corners were impossible, if not very inefficient to produce.
Solution # 1
The key to this issue is as much software related as it is tooling, and any solution must include effective communication between tool designers and software programmers. The obvious solution to create a smaller radius in the corners is to use a smaller diameter tool. However, this can lead to dramatically increased cycle time which can be prohibitive from a production stand point. Primitive software made it necessary to have all tools do a complete pass around the door profile, but modern systems allow the smaller diameter tools to isolate all four corners after the larger profile tools have done their work. The key is to start with a large profile tool to remove the majority of material and then break up the profile into small sections, and design the smallest diameter tool possible to clean the corners.
It is important to understand the limitations of the smaller diameter tools, and adjust feed rates and RPM accordingly to avoid tool breakage. The smaller diameter tools will often be designed with single flutes, so a drop in feed rate will also ensure better cut quality. Many small carving tools are better suited to solid carbide or carbide insert, rather than diamond due to design constraints.
Any tool inventory must include larger diameter tools for maximum material removal at higher feed rates, and matching tools with the smallest possible diameter to perform critical detailed carving applications in the corner of inside door profiles.
Problems # 2 – Surface finish
MDF is generally very consistent and easy to finish on the outside of the panel, but profiling on the inside of the panel can create a surface that is very difficult to finish due to machining lines and “fiber tearout”. MDF is obviously a porous material that tends to show loose fibers when machined in the core of the board. The density of MDF panel can have a dramatic impact on the resulting cut quality, but regardless of the quality of MDF it is impossible to achieve a surface finish in the core that is equivalent to the outside layer
Flat surfacing on the inside door panels is notoriously difficult as tools tend to leave machining lines on the overlapping tool path. Depending on the fiber size in the core, tools can also pull fibers which creates a pitted affect that must be filled by primmer. If fibers are not sheared off, they tend to raise up during priming, resulting in additional sanding or priming required.
Solution # 2
There are some machine parameter adjustments that can be made to improve surface finish. Smaller chiploads will obviously provide less feathering of fibers, but excessively small chiploads will cause heat generation and reduced tool life, so feed rate reduction is not always ideal. The solution lies in the tool design and cutting edge geometry.

Shows an example of a diamond surfacing tool designed to provide premium surface finish on MDF door panels. Notice the “Integrated” tool holder and tool body, which ensures optimal performance and allows tool to remove material at higher feed rates without sacrificing cut quality
The cutting edge geometry helps limit “overlap lines” between tool passes which reduces the amount of sanding required before priming. Up shear geometry helps extract large chip loads at higher feed rates to reduce cycle time. The diamond cutting edge is critical to providing prolonged tool life in difficult surfacing applications that produce excessive heat generation and cutting edge wear. To achieve optimal results, it is best to run multiple tool passes and leave 3-4 mm for the final finishing pass.
Cabinet doors will always be the focal point of any kitchen, and generally require the most attention to detail. Proper tooling design and application can help ensure the customer’s expectations are met, but also ensure that production cycle times and finishing costs are controlled. Consult your tool designers to discover many creative ways to make your MDF doors look as good as wood.
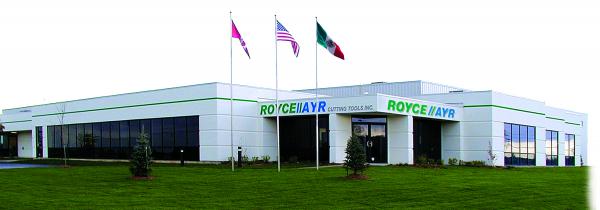
For over 4 decades Royce//Ayr has combined excellent customer service with state of the art cutting tool technology.
Royce//Ayr started out in 1963 as “Royce Carbide Tools Ltd” a small local sharpening shop for woodworking tools. The company soon became involved in the design and manufacture of specialty saw blades and cutters. In the ‘80s and ‘90s Royce started to explore the many possibilities of Insert and PCD-Diamond tooling.
1997 saw the merge of Royce Carbide Tools Ltd. with Ayr Saw & Tool Inc., a manufacturer of HSS saw blades for metal. This merger added valuable experience to the new company Royce//Ayr Cutting Tools Inc. In 2003 the company moved to a new 40,000 sq.ft. facility at 405 Sheldon Drive in Cambridge, ON.
As the industry is constantly changing and looking for better and faster ways to produce their finished products Royce//Ayr is committed to continuously investing in state of the art equipment and highly skilled employees to satisfy the demands placed on them.
Browse through this web site and inform yourself of our capabilities to produce premium quality cutting tools to internationally accepted ISO standards. You can always reach our dedicated sales and engineering staff to help design and develop the best custom tools to meet your specific needs.
With such excellent customer service and quality tooling, it’s no wonder that today Royce//Ayr is a leading manufacturer of cutting tools for wood, plastics, rubber and metal today.
Mission Statement
Royce//Ayr is committed to supplying customers with superior quality tools, excellent customer service and on-time delivery by employing cutting edge technology, tooling and machinery, and experienced dedicated employees.