
Thermwood has taken a major step toward its goal of 3D printing autoclave capable tooling from high temperature carbon fiber filled thermoplastic materials.
As an added benefit, Thermwood believes it will soon produce molds and tooling that function properly under vacuum in a heated, pressurized autoclave without the use of any type of coating to seal the printed tools.
50% Carbon Fiber filled PPS Panels Tested by Fleet Readiness Center
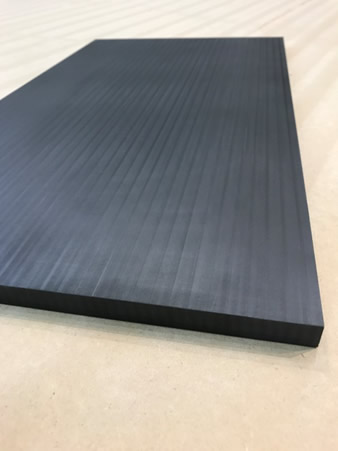
50% Carbon Fiber Filled PPS Panel Printed and Machined on LSAM
Working toward this goal, Thermwood engineers have printed 50% Carbon Fiber filled PPS panels on its LSAM additive manufacturing machine that held vacuum to an industry acceptable level in independent testing. The test was conducted by the Fleet Readiness Center, FRC-East, located at MCAS Cherry Point, NC under a previously announced Cooperative Research and Development Agreement (CRADA) partnership, and the results met FRC-East acceptance criterion that the bag must not lose more than 2 in Hg over 5 minutes.
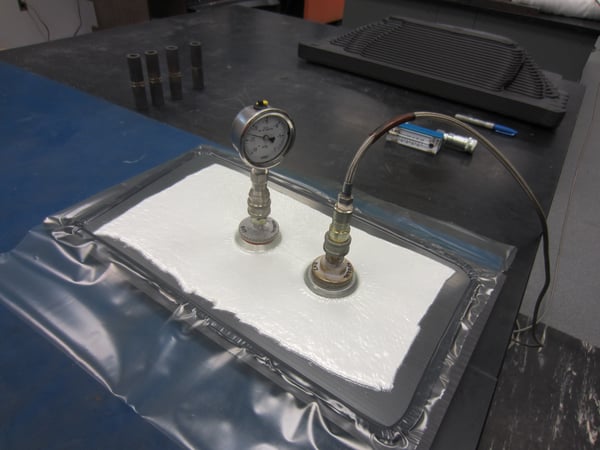
View of LSAM PPS Sample with Vacuum Bag
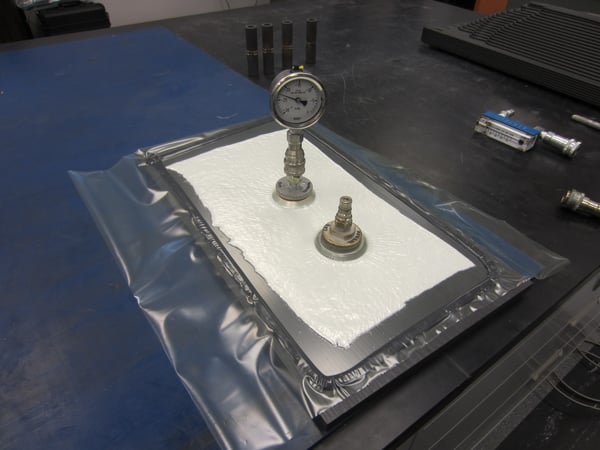
Previously, other unaffiliated companies have tested actual tools printed by Thermwood from 20% Carbon Fiber filled ABS and have also found that those tools held vacuum to an acceptable level without the use of any sealer or coating; however, the ABS material is not suitable for high temperature applications.
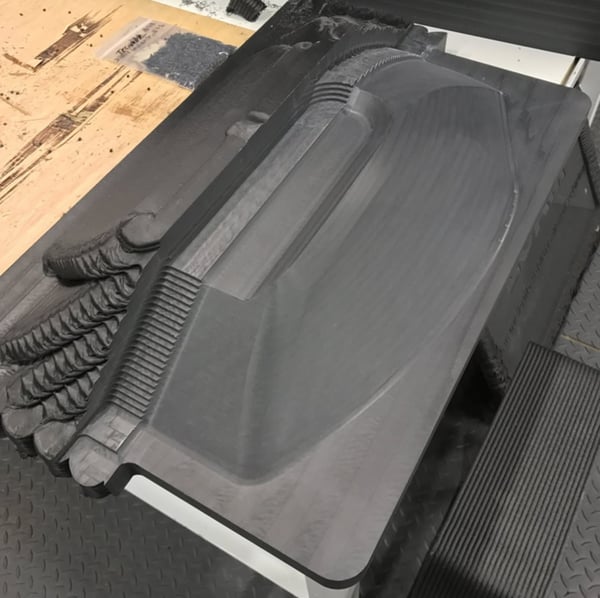
LSAM ABS Demonstration Part showing as printed (rough cut and finished surfaces)
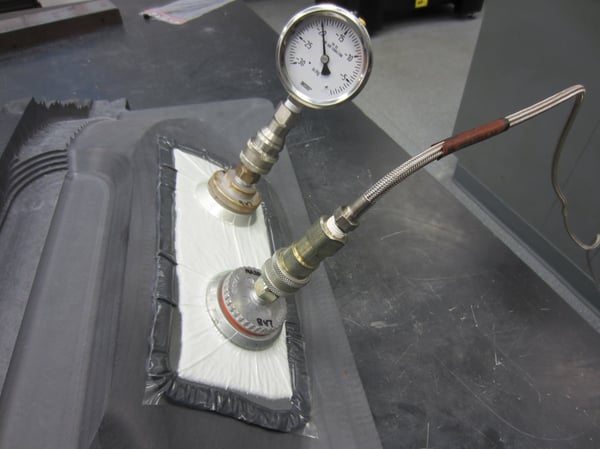
Vacuum Bagging Test on LSAM ABS Demonstration Part at Fleet Readiness
Despite that, several parts have been made from those tools under vacuum at room temperature and at slightly elevated temperatures. Thermwood has also already printed a 50% Carbon Fiber filled three dimensional PPS mold which has not yet been tested. Thermwood’s goal is to produce molds that will be used in a production autoclave, molding finished parts suitable for actual end use.
Thermwood's Additive Printing Process
Thermwood’s additive printing process differs fundamentally from conventional Fused Deposition Modeling (FDM) printing. Most FDM processes print parts by melting and extruding a relatively small bead of thermoplastic material onto a heated build platin that is contained within a heated chamber. The heated chamber keeps the extruded material from cooling too much before the next layer is added.
Thermwood machines print a large bead at such a high rate that a heated environment is not needed. It is basically an exercise in controlled cooling. Print speed is adjusted so that each layer cools to the proper temperature just as the next layer starts to print resulting in a continuous printing process that produces high quality parts. Thermwood believes this fundamentally different approach produces superior parts.
Thermwood's Patent Pending Compression Roller
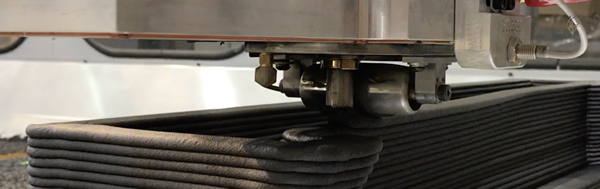
One other feature that Thermwood engineers believe helps produce solid, void free parts, is a patent pending compression roller that follows directly behind the print nozzle, flattening the bead while fusing it tightly to the previous layer.
More About LSAM
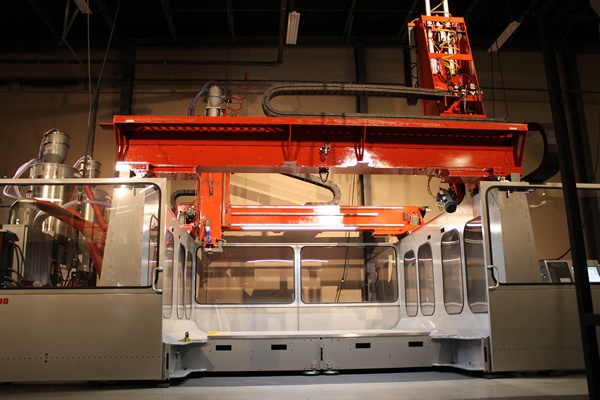
Thermwood’s large scale dual gantry LSAM machines both print and trim parts on the same machine. They are programmed with Thermwood’s LSAM Print 3D slicing software, which is rapidly becoming the most capable additive manufacturing software in the industry.
The LSAM and its software operate within Mastercam and are specifically designed for near-net-shape, rather than net-shape printing.
It works with most major CAD file formats including virtually all solid, surface and mesh formats. Thermwood maintains a continuing software development effort to continuously improve, enhance and expand its features and capabilities.