New Print Head Design for LSAM
Thermwood Corporation has unveiled a new design for the print head on its large scale additive manufacturing machines which it calls LSAM, (pronounced L-Sam). This new “Universal” design print head can be equipped with any of three interchangeable “Melt Cores”.
The print head is large by industry standards, being over 10 feet long and weighing one and a half tons, but despite the size and weight it moves at speeds up to five feet per second. The print head is designed so that the “Melt Core”, which consists of a feed housing, extruder and polymer melt pump, can be changed should higher or lower print rates be required.
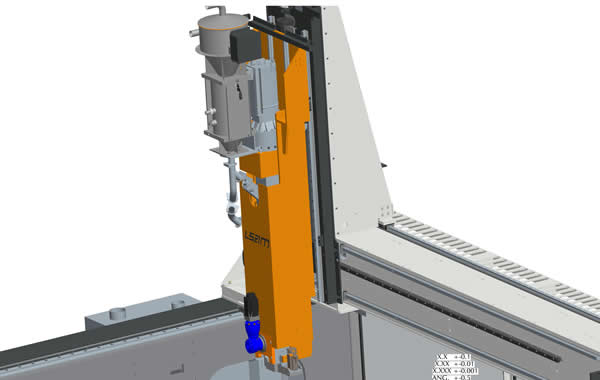
Universal Print Head Installed on LSAM Development Machine
Thermwood has installed a universal print head on its current 10’ x 10’ LSAM development machine with a 40mm Melt Core and has successfully printed composite tooling masters from 20% Carbon Fiber filled ABS, and has printed actual autoclave tooling from both 50% Carbon fiber filled PPS and 20% Carbon Fiber filled Ultem using this print head.
LSAM is DIfferent Than Other Thermoplastic 3D Printers
The print head is a critical element in Thermwood’s additive manufacturing process which functions differently than other FDM thermoplastic 3D printers. Most thermoplastic additive manufacturing systems print with a relatively small print bead onto a heated table in a heated environment. The heated environment is needed to keep newly printed layers from getting too cool to properly fuse with subsequent layers.
In Thermwood’s approach, the only heat source is the print head itself. A heated environment isn’t required. The process prints a large bead at such high output rates that the printed layer must be cooled rather than heated to achieve the proper layer to layer fusing temperature. The entire process is essentially an exercise in controlled cooling and produces large size, high quality, virtually void free printed structures.
Each layer is printed at a rate that allows it to cool to the ideal temperature before the next layer is applied. If the layer becomes too hot, print speed is reduced to allow more cooling time. If it becomes too cool, print speed is increased to reduce cooling time.
Real-Time Thermographic Image Display
A built-in thermographic imaging system displays a real time thermal image on the CNC control screen which aides the operator in achieving and maintaining the ideal print temperature during the print process.
Temperature Control Module Integrated into LSAM
The LSAM Universal Print Head can process material at temperatures up to 450oC. It uses an electronic temperature control module integrated within the print gantry CNC control, allowing full integration of temperature and pressure control with exclusive features of Thermwood’s print gantry CNC control, better supporting processes unique to 3D printing.
Three Melt Core Choices for LSAM
Thermwood offers three melt cores for its print head, each with a different maximum print rate. The maximum print rate determines the longest bead that can be printed during the available cooling time between layers. This cooling time varies depending on material, amount of fan cooling and geometric shape of the layer, but the faster the print rate the more material that can be laid down within the cooling time between layers, so faster print heads allow larger parts to be printed, but don’t really print parts faster.
Fastest Printing With LSAM
Even the standard 40mm LSAM melt core is generally so fast that it must be slowed on most parts to keep from printing a layer so fast that it doesn’t have sufficient time to cool properly between layers. In this case, often multiple parts can be printed in the same time it takes to print just one.
The LSAM machine is equipped with a standard 40mm Melt Core which includes a patented 40mm high speed extrusion screw coupled to a corresponding melt pump and deposition head. This standard configuration processes over 200 pounds of material an hour, depending on the specific material and is suitable for parts that have a print layer lap length of up to 200 feet while printing a standard bead that is .200 inch thick and .830 inch wide. This configuration has proven more than adequate for virtually all large parts today.
If even longer layer bead lengths are required, higher output Melt Cores are available. A 60mm Melt Core can process 50% more and a 70mm Melt Core has operated at rates of over 500 pounds per hour, which Thermwood expects to increase.
The fastest speed at which a part can be printed is determined by the cooling time required to reach the proper bonding temperature between layers and not by the output of the print head. Larger print head outputs simply allow larger parts to be printed within the cooling time between layers.
High output melt cores do, however, have a minimum operating speed so may not be suitable for smaller parts. If both small and really large parts are required on the same machine, the melt core can be changed from one size to another in less than a shift.
New 10'x20' Demonstration LSAM Under Construction
This print head will be installed on a new 10’ x 20’ demonstration machine currently under construction at Thermwood. Production machines come standard with the 40mm Melt Core.
Thermwood’s LSAM machines both print and trim on the same machine using separate gantries. The new approach to print head design adds even more flexibility.
LSAM Produces Solid, Void-free Parts
Using this technology, Thermwood has been able to produce large tools that are solid and void free enough to maintain vacuum without sealing or surface coating. This simplifies production of the tool, allowing accurate machining of the surface without having to deal with distortions that might be caused by variations in the thickness of a coating.
Print and Trim on the Same Machine
Thermwood offers a line of dual gantry additive manufacturing machines which both print and trim parts on the same machine. These machines can be up to 100 feet long with print head output rates from 150 to 500 pounds per hour.
The Thermwood LSAM is used to produce large to very large sized components from reinforced thermoplastic composite materials.
Although suitable for producing a wide variety of components, Thermwood is focusing on producing industrial tooling, masters, patterns, molds and production fixtures for a variety of industries including aerospace, automotive, foundry and boating.