
The Thermwood Cut Center is all about saving you time and money, using an easy to operate and sophisticated combination of software and machinery that you can feel confident in.
We've taken the fear out of automation by combining our easy to use interface and years of experience in the industry to create a powerful tool that will allow you to focus more on your products, business, making money, and worry less about being intimidated by the technical details. Your time is money, and the Cut Center helps you save more of both.
Below, find out just what makes the Thermwood Cut Center so special and profitable:
1. Huge Product Line From Day One
The product offering on the Thermwood Cut Center is extensive, and constantly growing. It includes cabinets, closets, furniture, doors, drawers, moldings and much more, and the sizes can easily be changed with no programming.
With a Cut Center, you can:
- Make your products with little effort
- Make your competitors products with little effort
- Expand your current offering to other profitable products with little effort
- Profit from an ever-expanding product line with no programming
We can also help you develop custom libraries for your specific product(s) in the size range and material you want and install them in your machine.
2. Virtually Instant Start Up
It is likely you will be in full production with a Thermwood Cut Center in about a half a day.
A typical CNC router can take as much as six months to program and get to that point. A half a day or a half a year? There is serious cost associated with that half a year.
With the Cut Center, it is all figured out for you, and from Day One you get:
- No programming
- No extensive training required
- No tooling to figure out and buy
- No cutting parameters to figure out
3. Feel Confident That the Details are Taken Care Of
The Thermwood Cut Center is engineered and programmed by experts who have taken all of the worry and headaches out of the equation. This gives you the confidence and peace of mind to focus on what is important - making money! You can concentrate on your product (its configuration, material and dimensions), as well as marketing and growing your business.
All the technical knowledge needed to make the machine work is already in place and invisible to the user - no new technical skills are necessary. You simply select what you want to make, right at the machine, and it makes it.
Running a Cut Center is much easier than a typical CNC router:
- It manages tools for you
- Figures out which tools to use for each job
- Figures out proper cutting speeds
- Tracks tool life
- It recovers from problems easily and smoothly
- Easily remake damaged parts by simply scanning a label
- Recover from broken tool(s) without scrapping parts
- Easily recut a defective sheet
- It manages maintenance
- It tells you when to clean filters
- It tells you when to lubricate
- It easily connects you to a service tech if you ever need more help
4. Constant Updates and Additions
We are constantly adding new libraries, features and capabilities to the Award-Winning Cut Ready Cut Center.
For instance, our latest update ads:
- Edge Banding Adjustment Ability
- Additional Shapes and Frames
- Dozens of new moldings and profiles
- A Cut/Line Editor to quickly and easily create lines and arcs
- A complete line of Vertical (Murphy) Wall Beds
5. Also Operate As a CNC Router
You can also operate the Cut Center system as a CNC router in the traditional manner, running programs generated with virtually any CNC software.
It is simple to switch between operating as a CNC router and operating as a Cut Center to assure that all machine parameters are properly reset and that the standard Cut Center tooling is properly installed, checked and ready to run.
6. With Other CNC Routers - Programming Required?
Every CNC router, regardless of price, has one thing in common..it must be programmed. You will need a CNC programmer. You will also need an operator with knowledge of tooling, feed speeds and holddown.
This programming and operating knowledge takes a lot of time and experience to master. That can be time away from running your machine and making money.
7. Other CNC Routers - Not So Cheap After All
A typical CNC programmer will cost you more each month than the payment on a Thermwood Cut Center, which does not need CNC programs or CNC programmers.
So, even if a machine was FREE, it would still cost you more than a Thermwood Cut Center, and in a few years the Cut Center payments go away while your programmer costs most likely will go up.
When you consider everything, a cheap router isn’t so cheap after all. In fact, some CNC router manufacturers will charge 3-5 times more for spare parts and service.
In these cases, the manufacturers plan is to double or triple their profit over 5 years through spare parts and service. This is why the initial cost of the CNC router is cheaper.
You are going to spend the money anyway...what will you have to show for it?
- With another direction you will need extensive training
- With any other direction, you will spend a lot of time programming a highly limited product offering
- With any other direction, someone will need to develop programs virtually every day (either you or someone you hire)
- With any other direction, you will produce less each day, because it is more complicated
- With any other direction, you will spend more and get less.
8. Buying a Cut Center vs. Buying a Typical CNC router
With a Cut Center, you don't need any extensive training, specialized knowledge or expensive employees to get started. Everything is already set up for you to succeed.
Items you will need to learn (or hire someone who knows) to operate a typical CNC router:
- G & M Code Programming
- Tooling
- Maintenance
- Fixturing
- Scrap Recovery
- File Handling
- Software(s)
9. Absolute Commitment to Your Success
Thermwood is committed to you and your success. We want you to love your new Cut Center, and for it to help move your business to the next level.
We have the best service and support in the business, and help is available with a push of a button on your Cut Center. We also have free phone, email and forum support. In addition, we are available to help you create custom libraries for your projects to quickly get you going.
10. Powerful Testimonials From Some Of Our Customers...

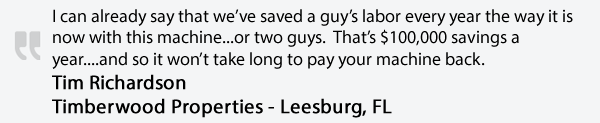
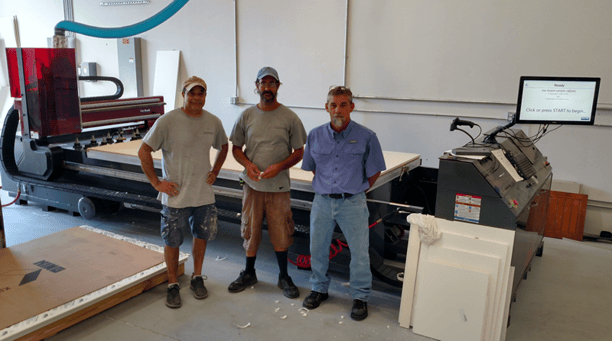
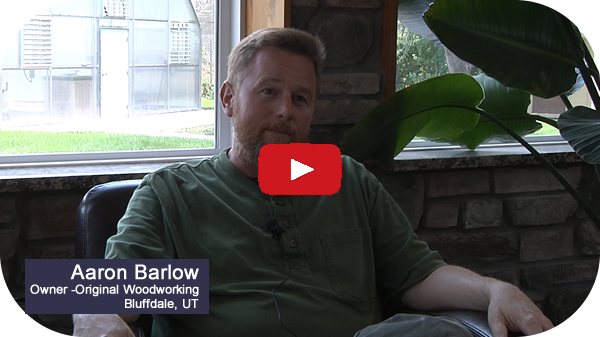
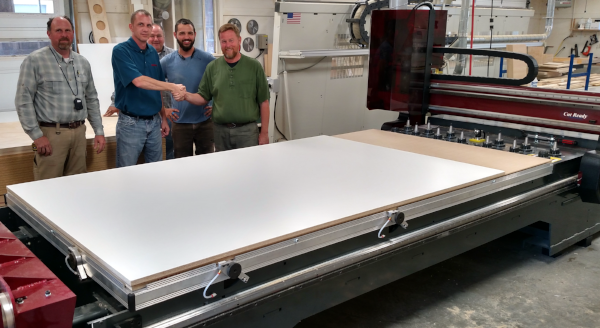
The Bottom Line...
Don't have extensive programming experience? Have programming experience and want both the flexibility of a CNC router and the ease of use of a Cut Center? Looking for a machine that will grow with your business? Then Thermwood's Cut Ready Cut Center might just be the machine for you.
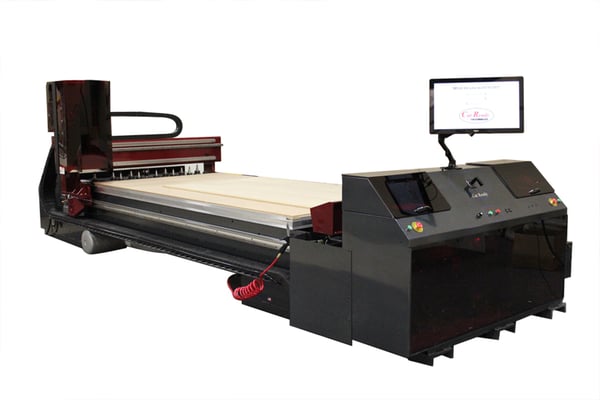
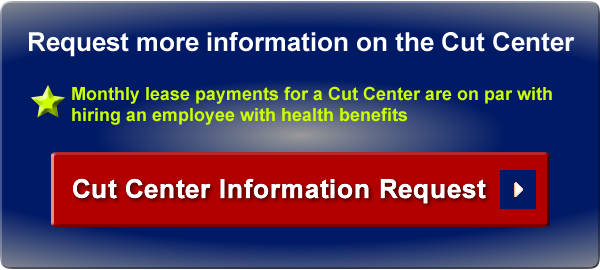