At its 50th Anniversary Gala Open House, Thermwood introduced and demonstrated an all new LSAM additive manufacturing machine model, offering even more choices for large scale additive manufacturing applications. Called LSAM MT, the new machine offers an all new configuration and significant advantages in certain applications.
Crowds watch the LSAM MT demonstration at the Thermwood 50th Anniversary Gala Open House
Video
Please click below to see a video of the LSAM MT in action!
The Details
Unlike standard LSAM systems, which feature dual gantries operating over a large fixed table, the MT (which stands for “Moving Table”) features a single fixed gantry mounted over a moving table. Available with a 10x10 foot table, this configuration offers several significant advantages, not the least of which is a dramatically lower price.
Despite the lower price, the LSAM MT is still a massive, robust industrial production machine capable of reliable, day in and day out production. Unlike standard LSAM systems, the MT can be configured as a “Print Only” machine. The logic for this is simple.
Despite the lower price, the LSAM MT is still a massive, robust industrial production machine
New Options
Near net shape printed tools dramatically reduce machining time for many companies currently machining tools from solid blocks of material. This frees up significant machining capacity which is already purchased and installed. For these companies, it makes no sense to purchase additional machining capacity with their additive system, since the change to additive frees up more than enough existing capacity to handle everything they can print. With this in mind, Thermwood decided to offer both “Print and Trim” and a “Print Only” versions of the MT.
The MT is available with a 10 foot by 10 foot table. The 10 x 10 machine actually has a 10 x 12 foot table with a 10 x 10 working area. The extra 2 foot is used to mount an optional Vertical Layer Print table. The 10 x 10 foot MT can be equipped with a new version of Thermwood’s patented Vertical Layer Printing technology. This means that it can make parts up to 10'x10' by 5 foot high using traditional Horizontal Layer Printing or, 5'x10' by 10 foot high using Vertical Layer Printing.
Since the print technology and print heads used on the MT are the same as used on the larger machines it offers the same throughput, print quality and layer to layer fusion that has made LSAM the leader in large scale additive manufacturing. As with the larger systems, the MT can process high temperature polymers which are ideal for autoclave capable tooling or compression molds for thermoset materials.
The large demonstration part printed at the open house is one of twenty similar parts which when combined become a production mold for a large yacht hull
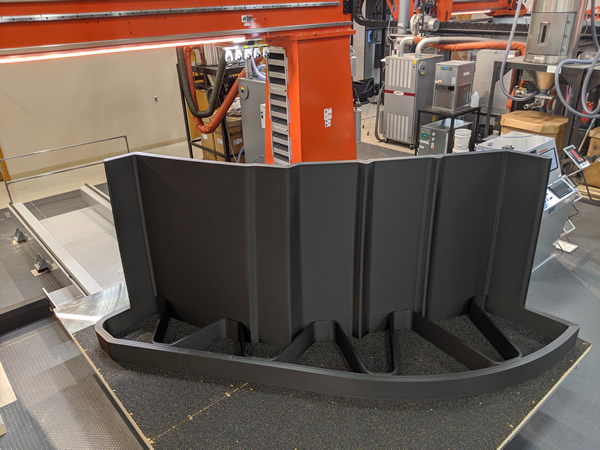
With the same print technology as used on the larger LSAM machines, the MT offers the same throughput, print quality and layer to layer fusion that has made LSAM the leader in large scale additive manufacturing
The LSAM MT is the ideal additive machine for a variety of exciting new applications
Things to Consider
With the addition of the MT, selecting the best size and configuration for an LSAM may not be quite as straightforward as it first appears. It depends on two major factors plus some additional considerations. The major factors are the material being printed and the size of the parts needed. Of these two, the material being printed is the most significant.
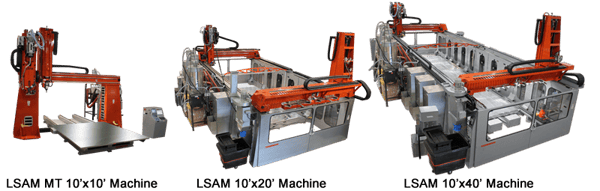
Thermwood offers a full line of LSAM sizes to fit almost any application
For purposes of machine selection, reinforced thermoplastic composite materials for room temperature or low temperature applications such as foundry patterns, boat plugs, boat and yacht molds, building structures and the like can generally be bonded securely with a variety of industrial adhesives. For these type of parts, even for really large parts, the smaller less expensive machine may be a better choice. The part can be separated into sections which can be printed individually and bonded into the final, potentially extremely large structure.
Although it seems counter-intuitive, this approach can be faster than printing the large structure as a single piece on a larger, more expensive machine. To better understand this we turn to the basics of the print process. Additive manufactured parts are printed in layers. The speed at which a layer can be printed depends primarily on how long it takes for the polymer being printed to cool enough to support the next layer. This layer cooling time depends on the polymer and is not affected by the size of the part. Each layer of a particular polymer takes the same amount of time, regardless of how big it is.
LSAM print heads can print faster, sometimes significantly faster than needed for most parts. Often it can print two three or more parts in the cooling time required for each layer. The large machine is only printing a single part, one layer at a time, making it two or three time slower. To print the part in one piece, the large machine must operate continuously, around the clock, sometimes for days. This is not a problem for factories that operate on all three shifts but can present staffing problems for single shift operations. With the MT, several different segments of the same part can often be printed in a single shift. Depending on the item being printed, it is possible to print as much in a single shift as the large machine, printing a single part, can do in 24 hours.
For large parts made from bondable materials, often the smaller, less expensive machine is a better choice.
Materials intended for high temperature applications, PSU, PESU, PEI, Ultem, etc. generally are resistant enough to solvents that they can’t be effectively bonded. Even if they could, few if any, adhesives exist that can withstand the operating temperature or the thermal cycling these materials experience. For these applications, the machine needs to be large enough to print the part in one piece, even though it could be slower. This is where larger machine configurations are needed. The larger machines also offer the ability to print and trim at the same time, which may be beneficial in some circumstances.
Since the print heads are the same on all Thermwood LSAMs, the smaller MT can be used for these high temperature parts, provided they fit in the available envelope.
Just like the standard LSAMs, the MT comes complete, fully engineered with everything needed for production operation.
About Thermwood Corporation
Thermwood is a US based, multinational, diversified CNC machinery manufacturer that markets its products and services through offices in 11 countries. Thermwood is the oldest manufacturer of highly flexible 3 & 5 axis high-speed machining centers known as CNC routers.
Thermwood has also become the technology and market leader in large scale additive manufacturing systems for thermoplastic composite molds, tooling, patterns and parts with its line of LSAM (Large Scale Additive Manufacturing) machines that both 3D print and trim on the same machine. These are some of the largest and most capable additive manufacturing systems ever produced and are marketed to major companies in the aerospace, marine, automotive and foundry industries as well as military, government and defense contractors.
10’ x 10’ LSAM MT (Large Scale Additive Manufacturing) |
