CNC router or Cut Center...Which is Better for Me?
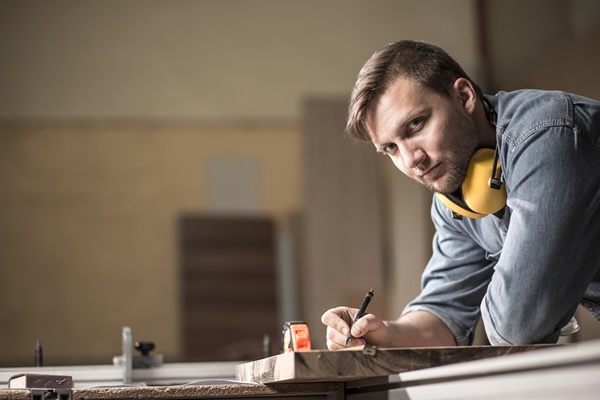
Nested based manufacturing and CNC routers are well known to most cabinetmakers. Thermwood Cut Centers, less so, but there is a big difference between the two, even though they produce essentially the same products. This difference means that cabinetmakers wanting to automate must make a decision. Which direction is better for them?
The major difference between a CNC router and a Thermwood Cut Center is in who addresses the details of each cabinet design and how involved the user must be in the underlying technology.
CNC router - the Basics
A CNC router system consists of three fundamental elements:
- A PC computer able to run sophisticated software
- A cabinet design software package that can produce the required CNC programs
- A machine to execute the CNC programs.
With a traditional CNC router system, the user designs the cabinets and addresses all of the design details. They must also become intimately involved with the underlying technology. They are responsible for selecting, installing, learning and running the software.
They must also understand the intricacies of the machine control and operation so that their programs run properly. They must adjust and maintain machine parameters, select and set up tooling and deal with vacuum hold down and the spoilboard.
Thermwood Cut Center - What you need to know
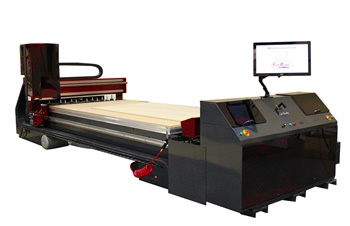
A Thermwood Cut Center consists of a single element - the machine. It already knows how to make cabinets, closets, furniture, doors, drawers and much more just about any way you want.
It doesn’t require you to learn complex programming to operate, and is so user-friendly that it walks you through every step of the process. You simply tell the machine what you want to make via an easy to use touch screen interface, and it does it. No programming is required.
Other Thermwood Cut Center Features
With a Thermwood Cut Center, details of the cabinet design have already been addressed by experienced and seasoned programmers, working with professional cabinetmakers and have been built into the machine. You need have no more involvement with the underlying technology of a Thermwood Cut Center than you do with the underlying technology of your car.
- The system has been automated and refined to handle areas such as tooling and tool life, vacuum hold down and spoilboard maintenance, error handling and routing maintenance without the user becoming directly involved. The machine guides you, step by step, can show a quick instructional video of every step and can connect with a real live person on the screen should you ever need help.
- Also, you can operate the Cut Center system as a CNC router in the traditional manner, running programs generated with virtually any CNC software. Thermwood has created a simple way to switch between operating as a CNC router and operating as a Cut Center to assure that all machine parameters are properly reset and that the standard Cut Center tooling is properly installed, checked and ready to run.
Watch to Learn the Differences Between a CNC Router and a Cut Center
The Main Differences
- A CNC router is completely flexible, totally controlled by the user who must become directly involved with both the software and hardware.
- A Thermwood Cut Center makes cabinets, etc that you select and define, and can be run by just about anyone. Two different approaches, so which is best for you?
The Three Types of Cabinetmakers
Those who like and embrace computers, software and technology.
They will only be happy if they have the total flexibility, capability and control of a CNC router and a powerful design software. Using the car analogy, this would be someone that builds custom or race cars. They also likely have the technical skill and experience needed to take full advantage of the possibilities of the underlying technology with little technical risk.
Those who really dislike technology.
They just don’t like it, and really can’t or won’t work with computers, parameters or software. They just want to make cabinets, etc. They are strictly woodworkers. Clearly the Thermwood Cut Center works better for them. It allows them to enjoy the financial benefits of automating without totally disrupting what they are used to. It could very well help them stay in business in an ever more competitive market.
Everybody else.
These shops are in business to make money by making cabinets. They neither love nor hate technology. It is simply something you learn in order to automate and make more money. The decision here is not as easy.
The Fine Details of Each Approach
If you compare the initial investment cost of the two approaches, they are about the same even though the Cut Center looks more expensive at first. In the end, you will spend about the same amount of money for either, although you will spend it in different places.

A Cut Center is tooled and ready to make cabinets on day one. For a fair comparison, with a CNC router investment, you must add the cost of a vacuum system, a design computer, design software, technical training for the software, technical training for the machine, programming time to create the cabinet programs and tooling. When you consider everything, your money investment will likely not be much different between the two systems, although you will likely have invested more time in getting the CNC router into production.
There is also a cost difference in operating the two systems that can tip the scales one way or another. A CNC router needs a CNC program for every job. This means it needs a programmer to create those programs. A CNC programmer will cost more each month than the total lease cost of a Cut Center. Also, after five years, the lease cost of a Cut Center becomes zero. Most likely the cost of a programmer will go up over the same period.
There is also the matter of technical risk. With a Cut Center technical risk is low. Everything has been developed, tested, refined and it is ready to make your products.
With a CNC router, everything needed to make it work from creating the CNC programs to selecting tooling is your responsibility. Clearly there is more technical risk with a CNC router.
Take a Walk Around Tour of the Cut Center
Another Factor

The Cut Center is set up to make a lot more than just basic kitchen cabinets. There are closet, bath and utility cabinets as well as furniture such as shelves and shelf walls, entertainment centers and entertainment walls. There are also drawers, slab and MDF doors and drawer fronts and custom sized moldings, both straight and arch. The selection is quite large and making any of these is quite easy.
If you don’t need these things, this may not be important, but with a Cut Center you can make a wide variety things with little effort. They are already in there. These things can also be made with a CNC router but only with significant additional investment in time and effort. Thermwood has invested thousands of hours in developing and testing these items. To duplicate them will require thousands of hours on your part.
From an operating standpoint, you do not need a computer, software or a software programmer for a Cut Center. Also, the machine operator does not need the same level of technical skill and training that is required to operate a CNC router.
See How Easy it is to Design a Cabinet and add it to the job
The Bottom Line
In the end, the decision is likely a philosophical and emotional decision since both systems offer the huge benefits of automating cabinet production. It is the learning curve that separates them.
The Thermwood Cut Center might be the machine for you if you don't have extensive programming experience or have experience and want both the flexibility of a CNC router and the ease of use of a Cut Center.
A CNC router might be for you if you have extensive programming experience and want the total flexibility, capability and control of a CNC router and a powerful design software.
See How Simple it is to Machine a Cabinet Job on the Cut Center
What our Cut Center Customers Think...
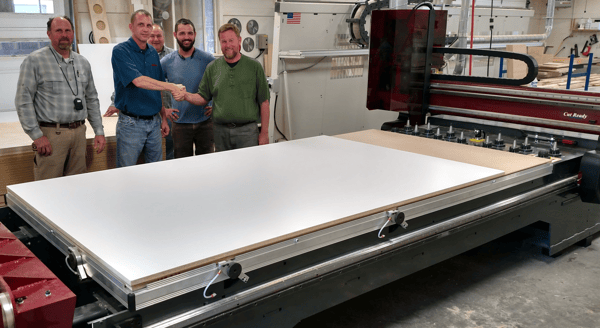
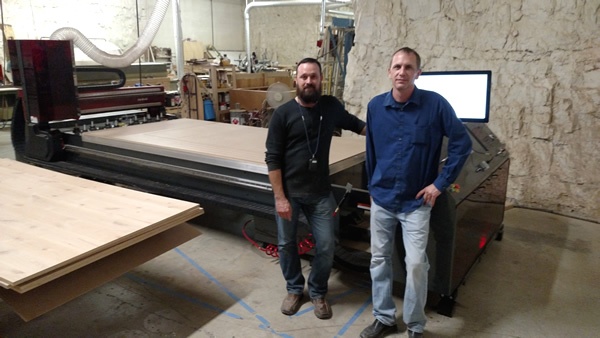
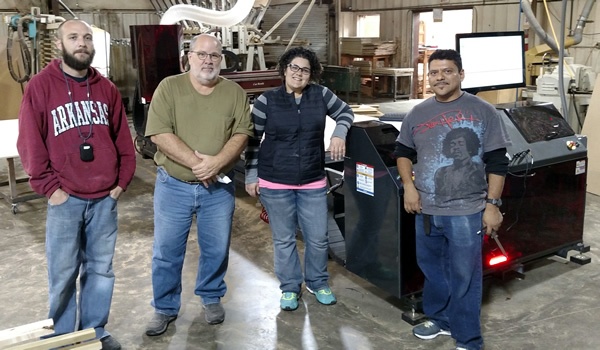
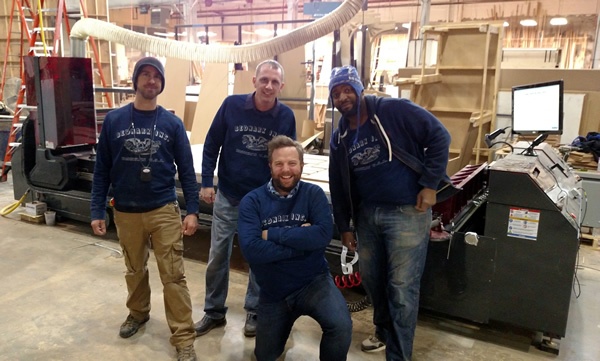
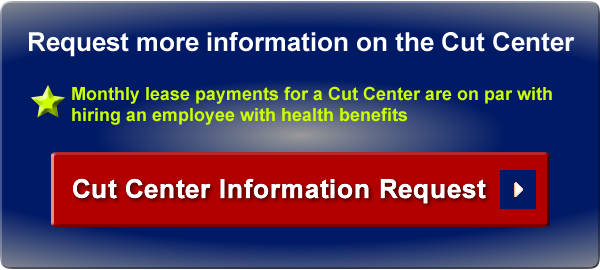