Thermwood Corporation, manufacturer of some of the largest composite thermoplastic additive manufacturing systems operating in industry today, has announced the availability of a new line of lower cost “print only” LSAM systems, called LSAM Additive Printers.
Thermwood’s current LSAM line of large scale, dual gantry, “print and trim”, near-net-shape additive manufacturing systems use an advanced print technology that produces high quality, fully fused products from a wide variety of reinforced composite thermoplastic polymers, including materials that process at high temperature like PSU, PESU, and PEI.
These systems are being used primarily to produce molds and tooling, most for aerospace and industrial production applications.
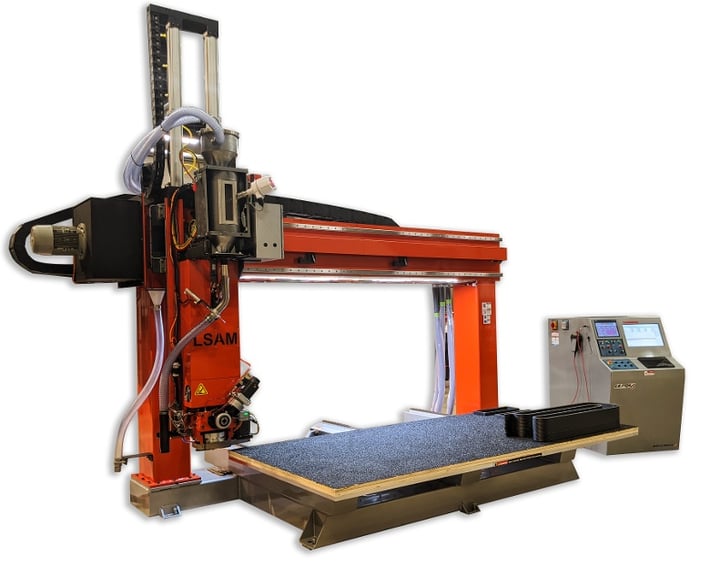
LSAM ADDITIVE PRINTER
Thermwood Corporation, manufacturer of some of the largest composite thermoplastic additive manufacturing systems operating in industry today, has announced the availability of a new line of lower cost “print only” LSAM systems, called LSAM Additive Printers.
Thermwood’s current LSAM line of large scale, dual gantry, “print and trim”, near-net-shape additive manufacturing systems use an advanced print technology that produces high quality, fully fused products from a wide variety of reinforced composite thermoplastic polymers, including materials that process at high temperature like PSU, PESU, and PEI.
These systems are being used primarily to produce molds and tooling, most for aerospace and industrial production applications.
SMALL BUT POWERFUL
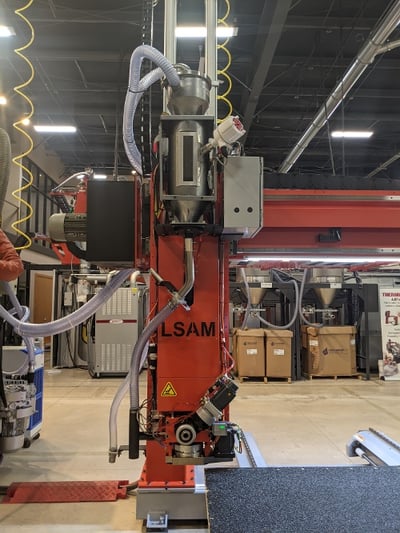
To accommodate the request for a lower cost system, Thermwood refined and updated the gantry structure of its highly successful 5 axis CNC routers. This machine was re-engineered to use the incredibly strong “slot and tab” structural steel approach used on flagship LSAM machines. The same table, base structure and servo drives used on their five axis CNC routers could be used pretty much as is. With these changes the “LSAM Additive Printer” was born.
Although smaller than the flagship systems, it is capable of producing large parts at temperatures up to 450° C, with overall size limited primarily by the table size and working envelope.
Available Sizes
The new LSAM Additive Printers are all fixed gantry, moving table designs with table sizes of 5’x5’ and 5’x10’ and are capable of printing parts up to 4’ high. The 5’x10’ machines are available in two styles, 5’ wide with 10’ of front to back motion or 10’ wide with 5’ of front to back motion. Maximum table print weight is 1,000 pounds, however, the 10’ wide 5’ deep machine is available with a dual servo drive which doubles the weight carrying capability. It is planned to equip the 5’ wide 10’ deep version with a Vertical Layer Printing option which will allow it to vertically print parts up to ten feet tall.
Trimming Printed Parts
For trimming printed parts, Thermwood recommends our new LSAM Additive Trimmer, which is available in the same table sizes as these new LSAM Additive Printers. It is available with up to 5’ of vertical travel, allowing it to trim completely around and over the top of the largest part the LSAM Additive Printer can print. As an added benefit, with both an LSAM Additive Printer and an LSAM Additive Trimmer, you can print and trim at the same time.
Although having a new LSAM Additive Printer plus an LSAM Additive Trimmer requires purchasing two machines, the combined cost of both is just over a third of the cost of an LSAM 1020 (which is currently the smallest flagship LSAM system that can both print and trim at the same time). The LSAM 1020 does have a much larger table, faster print head and the ability to do vertical layer printing up to 20 feet long, however, if you don’t need those capabilities, the new LSAM Additive Printers may be an answer. If you already have trim capability, the cost can be even lower.
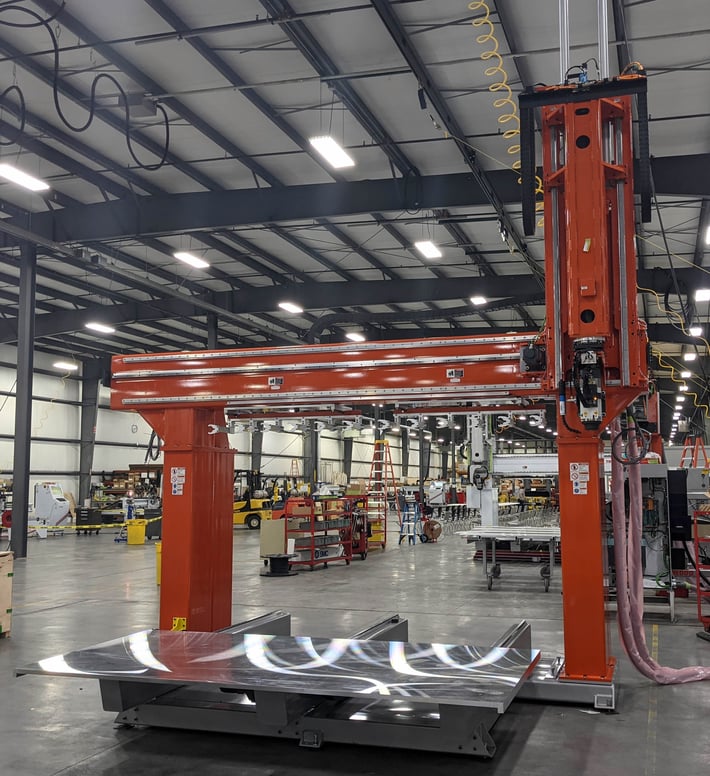
Same Powerful Features
The same powerful, feature rich LSAM control used on the large flagship LSAM systems, along with all its unique patented additive print features is standard on the new LSAM Additive Printers. A system for drying and conveying pelletized polymer material is also included as is a liquid chilling system to maintain temperature control on vital systems. This is especially important when processing high temperature materials.
Optional Enclosure
An optional enclosure that surrounds the machine is available. The machine with this full enclosure can also be built to meet European CE standards.
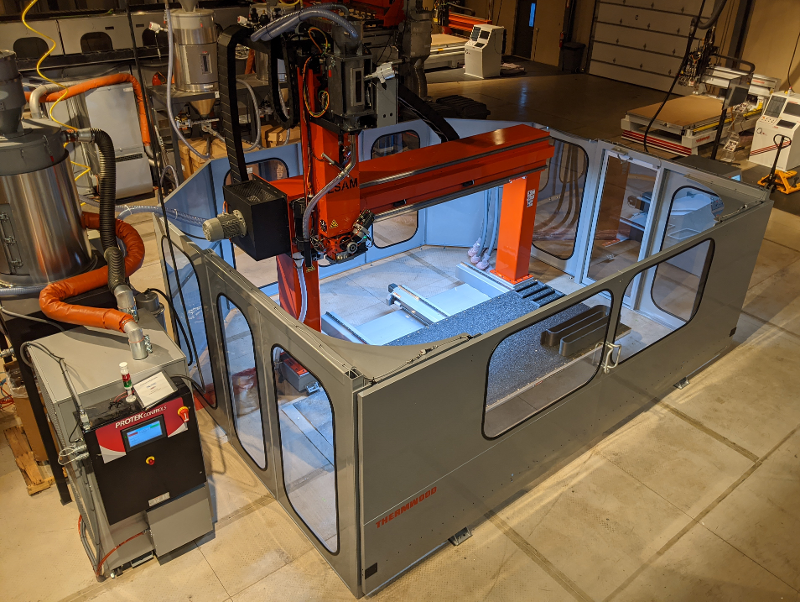
Optional Dual Hopper Dryer
The machine comes standard with a single hopper material dryer, however, an optional dual hopper dryer is also available for applications that change materials often.
Thermal Sensor Layer Automation System
Thermwood’s new Thermal Sensor Layer Automation System is also available on the LSAM Additive Printers. This is an exciting new system that automates the print process to easily and automatically obtain the highest quality layer to layer fusion.
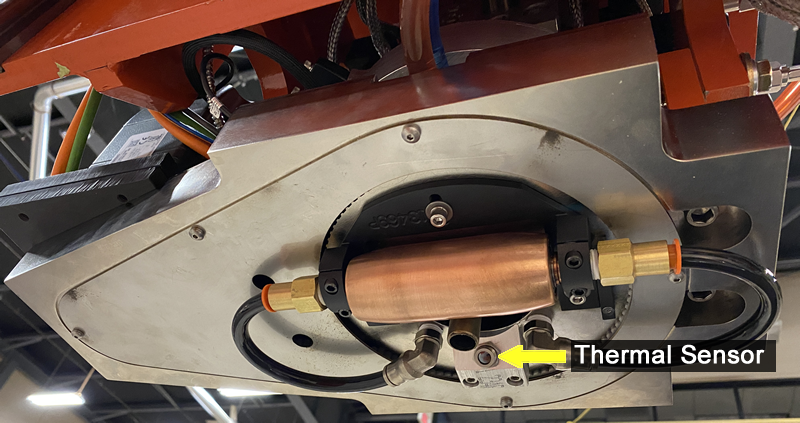
With this system, a servo controlled thermal sensor, which travels with and rotates around the print nozzle, measures the temperature of the bead an instant before a new bead is added. This data is sent to the control which automatically adjusts print speed to print at the precise temperature that results in the best bead fusion for that particular polymer. Thermwood’s
LSAM print technology already produces the best quality, strongest large scale additive parts and this system not only makes it better but also easier.
Same Powerful Print 3D Slicing Software
The same Thermwood LSAM Print 3D slicing software used on all the other LSAM systems is used to program LSAM Additive Printers. Several levels of software training are available.
The Bottom Line
This new LSAM Additive Printer is intended to introduce LSAM additive technology to a whole new level of application and customer. It targets companies that want to print top quality, large composite thermoplastic parts, but don’t really need, nor can they cost-justify, the really large LSAM systems. These new systems also target companies who already have sufficient trimming capability and may only need a quality print function. Applications include industrial fixtures, molds (including high temperature molds), tooling, foundry patterns, and hundreds, if not thousands of similar applications.
With the addition of the LSAM Additive Printers, Thermwood now offers the largest selection of large scale additive manufacturing systems for thermoplastic composite materials in the industry with models available for just about every application and budget.
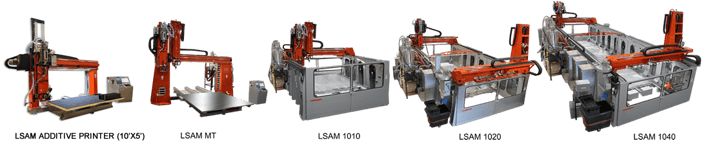
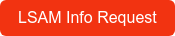